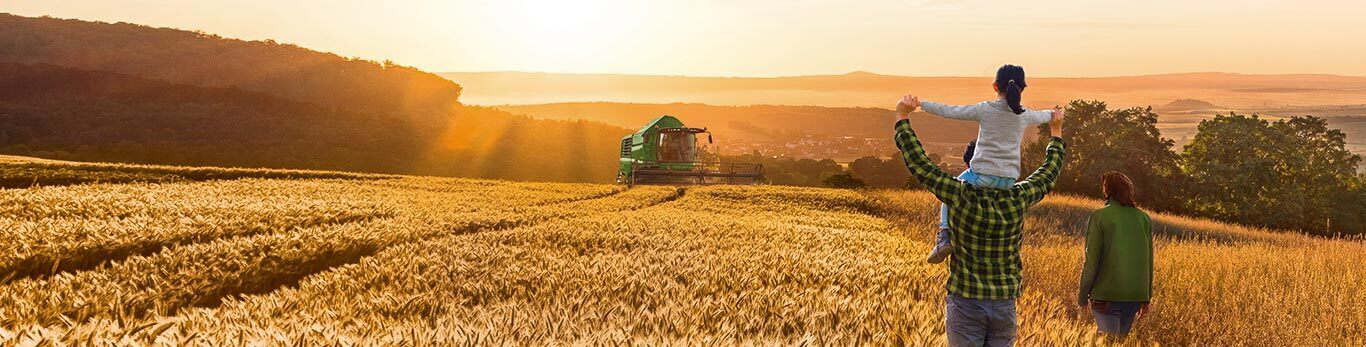
John Deere Financial offers you financing solutions that help you and your business succeed. Because of our customer focus and knowledge about John Deere machines, we understand your requirements around financing solutions better than anyone else.
Get to know more about John Deere Financial in Europe and the CIS.
Get to know more about your opportunities in Luxembourg.
John Deere Financial, more than 2.300 employees worldwide help our customers and their businesses to succeed.
John Deere Financial is one of the largest providers of financial services to agricultural and construction customers. We provide equipment financing to help facilitate the sale of John Deere agricultural, construction, forestry, turf, and utility equipment.
Deere & Company started providing equipment financing to its retail customers in the mid-19th century. Today, John Deere Financial offers retail finance programs in more than 50 countries.
Our mission at John Deere Financial is to enable our dealers and customers to invest into the latest John Deere technology, allowing them to run a more efficient and sustainable business. We achieve this as a diverse and highly engaged team that works with a high degree of autonomy in an international environment.
Visit the website of our official National Dealer, Cloos & Kraus, to find out more about John Deere products and services in Luxemburg.